Dynamic 3.0
We confirm receipt of noncommittal demand
Demanded machine: Dynamic 3.0
Company:
Kontaktní osoba:
VAT:
Adresa:
Phone:
E-mail:
Your inquiry:
Destination country:
We will contact you as soon as possible using given contact details.
Back to website
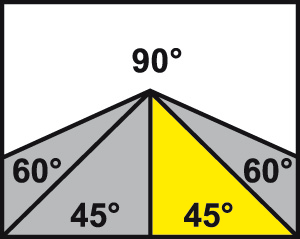
Simpler, affordable, yet extremely powerful, accurate and robust. This fully automated band saw with CNC finds general application in series cutting. The machine features proportionally controlled hydraulic material feed. The machine can be controlled in fully automatic, semi-automatic or manual mode. In manual mode all functions of the machine are controlled separately. The maximum length of a single feed is 500 mm. Continuous manual adjustment of the cut angle in the range of 90-45 °. The saw can cut material at an angle even in automatic mode. The hydraulically controlled robust feeding vice moves on hard-chrome bars. The linear measuring system guarantees high measuring accuracy. High feed speed controlled by proportional equipment, CNC-controlled acceleration and deceleration process helps achieve a feeding accuracy of 0.1 mm. Smooth deceleration in the end positions also prevents slippage of heavy materials.
The central control panel with a large colour touch screen (7.5") guarantees very easy control of the machine using a proprietary operating system. You only enter the desired length and quantity. Material clamping and the movement of the band saw arm to the cut and back to the desired position according to the material cross-section are also controlled hydraulically. Pressure control of the feeding vice and the fixed vice as standard. Maximum cutting efficiency is maintained also thanks to the possibility of setting optimum saw band rate by a frequency converter in the range between 15 and 90 m/min., which significantly contributes to cutting accuracy and service life of saw bands.
The maximum material feed accuracy results from the robust design of the machine with all main parts made of grey iron and the sturdy design of the feeding system. The base design and the entire sturdy structure ensure an exceptional stability of the machine, even when cutting heavy workpieces. The base is equipped with a large removable chip container and allows the installation of a screw chip conveyor. The 27x0.9 mm industrial saw band is produced in many variants and enables industrial splitting of a wide range of materials, including stainless steel or tool steel. The latest concept of the arm casting with cavities is fitted with running wheels with an optimal diameter. The larger diameter of the wheels ensures less bending stress of the saw band. All this ensures an outstanding rigidity of the whole system, long service life of saw bands and maximum cut precision. All electrical wiring and the coolant delivery system are concealed in hollow parts of the arm, which means they are protected from damage. The new concept of the arm also brings a great simplification when changing the saw band or when cleaning the inside of the arm. You just need to open the hinged back cover of the arm and it will stay locked in the upper position.
Apart from creating an entirely new design of the arm, we also made many technical adjustments and changes improving the quality, user comfort and service life of the machine. As an accessory, it is possible to use the cleaning brush of the saw band that is synchronously driven by the driving wheel. Simple intuitive control using ergonomically positioned controls on a separate central control panel. The very robust machine framework composed of grey iron castings guarantees safe vibration absorption. The modern concept of the band saw arm allows large cutting ranges in perpendicular as well as angular cuts. Optimal-diameter running wheels and precise three-side hardened steel blade guides ensure long service life of the band and cutting accuracy. The optimal fit of the running wheels, the tensioning system and all rotating parts increases the service life of the machine. Noiseless and maintenance-free drive of the saw band is provided by an industrial electric motor with a worm gearbox. Check of the correct tension or tear of the saw band. When the saw band breaks, the machine automatically stops. The machine is connected to a complete cooling system with a powerful pump, enabling separate flow control on both guide heads and another adjustable outlet. The emulsion tank with a powerful pump is located in the machine base.
90° | +45° | |
![]() |
300 | 240 |
![]() |
285 | 220 |
![]() |
300 x 220 | 235 x 150 |
Main motor | 400 V, 50 Hz, 2,2 kW |
Pump motor | 400 V, 50 Hz, 0,12 kW |
Hydraulic motor unit | 400 V, 50 Hz, 0,55 kW |
Feed rate of material | 1,8 / 4,2 / 6,6 m/min. |
Saw blade speed | 15-90 m/min. |
Working height of vice | 870 mm |
Hydraulic system oil | cca 26 l (ISO 6743/4-HM, DIN 51 524 part 2-HLP |
Coolant tank | cca 35 l |
Machine dimensions | Dimension drawing |
Machine weight | 940 kg |
-
Magnetic chip separator
For particularly fine chips that have passed through the sieves in the saw, a highly efficient magnetic separator is used. It saves time for cleaning and disassembling the cooling path and extends the service life of the cooling emulsion. This device is easily removable and easy to clean outside the machine by simply pulling the magnetic bars out of the housing.
The sawblade replacement
-
Simpler, affordable, yet extremely powerful, accurate and robust. This fully automated band saw with CNC finds general application in series cutting. The machine features proportionally controlled hydraulic material feed. The machine can be controlled in fully automatic, semi-automatic or manual mode. In manual mode all functions of the machine are controlled separately. The maximum length of a single feed is 500 mm. Continuous manual adjustment of the cut angle in the range of 90-45 °. The saw can cut material at an angle even in automatic mode. The hydraulically controlled robust feeding vice moves on hard-chrome bars. The linear measuring system guarantees high measuring accuracy. High feed speed controlled by proportional equipment, CNC-controlled acceleration and deceleration process helps achieve a feeding accuracy of 0.1 mm. Smooth deceleration in the end positions also prevents slippage of heavy materials.
The central control panel with a large colour touch screen (7.5") guarantees very easy control of the machine using a proprietary operating system. You only enter the desired length and quantity. Material clamping and the movement of the band saw arm to the cut and back to the desired position according to the material cross-section are also controlled hydraulically. Pressure control of the feeding vice and the fixed vice as standard. Maximum cutting efficiency is maintained also thanks to the possibility of setting optimum saw band rate by a frequency converter in the range between 15 and 90 m/min., which significantly contributes to cutting accuracy and service life of saw bands.
The maximum material feed accuracy results from the robust design of the machine with all main parts made of grey iron and the sturdy design of the feeding system. The base design and the entire sturdy structure ensure an exceptional stability of the machine, even when cutting heavy workpieces. The base is equipped with a large removable chip container and allows the installation of a screw chip conveyor. The 27x0.9 mm industrial saw band is produced in many variants and enables industrial splitting of a wide range of materials, including stainless steel or tool steel. The latest concept of the arm casting with cavities is fitted with running wheels with an optimal diameter. The larger diameter of the wheels ensures less bending stress of the saw band. All this ensures an outstanding rigidity of the whole system, long service life of saw bands and maximum cut precision. All electrical wiring and the coolant delivery system are concealed in hollow parts of the arm, which means they are protected from damage. The new concept of the arm also brings a great simplification when changing the saw band or when cleaning the inside of the arm. You just need to open the hinged back cover of the arm and it will stay locked in the upper position.
Apart from creating an entirely new design of the arm, we also made many technical adjustments and changes improving the quality, user comfort and service life of the machine. As an accessory, it is possible to use the cleaning brush of the saw band that is synchronously driven by the driving wheel. Simple intuitive control using ergonomically positioned controls on a separate central control panel. The very robust machine framework composed of grey iron castings guarantees safe vibration absorption. The modern concept of the band saw arm allows large cutting ranges in perpendicular as well as angular cuts. Optimal-diameter running wheels and precise three-side hardened steel blade guides ensure long service life of the band and cutting accuracy. The optimal fit of the running wheels, the tensioning system and all rotating parts increases the service life of the machine. Noiseless and maintenance-free drive of the saw band is provided by an industrial electric motor with a worm gearbox. Check of the correct tension or tear of the saw band. When the saw band breaks, the machine automatically stops. The machine is connected to a complete cooling system with a powerful pump, enabling separate flow control on both guide heads and another adjustable outlet. The emulsion tank with a powerful pump is located in the machine base.
-
90° +45° 300 240 285 220 300 x 220 235 x 150 Main motor 400 V, 50 Hz, 2,2 kW Pump motor 400 V, 50 Hz, 0,12 kW Hydraulic motor unit 400 V, 50 Hz, 0,55 kW Feed rate of material 1,8 / 4,2 / 6,6 m/min. Saw blade speed 15-90 m/min. Working height of vice 870 mm Hydraulic system oil cca 26 l (ISO 6743/4-HM, DIN 51 524 part 2-HLP Coolant tank cca 35 l Machine dimensions Dimension drawing Machine weight 940 kg -
-
-
Magnetic chip separator
For particularly fine chips that have passed through the sieves in the saw, a highly efficient magnetic separator is used. It saves time for cleaning and disassembling the cooling path and extends the service life of the cooling emulsion. This device is easily removable and easy to clean outside the machine by simply pulling the magnetic bars out of the housing.
-
The sawblade replacement